THERMOFORMING PROCESS
Heating
The first step consists of heating a sheet of plastic to make it malleable. This phase helps to achieve a high quality forming and optimizes forming cycle performance. Since plastics do not conduct heat well, it is vital to adjust the heating time based on the thickness of the sheet, the efficiency of the heating system, as well as the colour and nature of the material. The heat must be distributed evenly for an ideal result. Our experience at Thermoforme L.R. ensures that this phase is well respected.
Forming
Once the sheet has softened, it can be easily formed into the shape of the selected mould. Male (convex) and female (concave) moulds can be matched to obtain parts. The malleable plastic takes the shape of the mould and results in the desired shape. Thermoforme L.R. offers you the three main shaping techniques:
- Air evacuation: sheet sticks to the mould
- Air pressure: sheet is pressed against the mould
- Mechanical force
Cooling
Forming is followed by cooling and is an important step to obtain a uniform product. It's important to allow the part to properly cool so that it can be removed from the mould without warping, flaws or sticking. The hardening period depends on the thickness of the part and the efficiency of the cooling system. A transition period is required between cooling and cutting since the part shrinks at room temperature. This is the removal process. Rest assured, our staff at Thermoforme L.R. are very attentive to detail and make sure that parts are always completely cooled in order to guarantee the best results and impeccable products.
Cutting / trimming
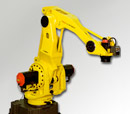
The last phase consists of finishing the parts, which is done by cutting or trimming your products. The Thermoforme L .R. facilities are equipped with high performance tools. Thanks to our Fanuc robot, we can drill and cut your parts quickly and precisely. This also increases the consistency of parts.